Reliability Engineer
NRG
(Gettysburg, Pennsylvania)NRG is the leading integrated power company in the U.S., built on the strength of the nation's largest and most diverse competitive electric generation portfolio and leading retail electricity platform. A Fortune 200 company, NRG creates value through best in class operations, reliable and efficient electric generation, and a retail platform serving residential and commercial businesses.
- Provides mechanical and process engineering expertise for pumps, heat recovery steam generators, turbines, generators, valves, etc. for Hunterstown Combined Cycle and Heritage Region CTs.
- Serves as the Environmental Specialist for Hunterstown Combined Cycle and Heritage Region CTs coordinating with corporate Environmental Department.
- Serves as champion for the Condition Based Maintenance (CBM) program including data collection, analysis, reporting and enrollment of staff.
- Serves as champion for the Predictive Maintenance (PdM) testing per company standards with expertise in oil analysis, vibration monitoring and thermography.
- Serves as the site Champion for CBM tools such as PI and SmartSignal.
- Serves as the site responsible person for coordination of Weld Repair Packages including the coordination of certified welders, pre-heat and post-heat services, and NDE testing. This person shall be versed in the AMSE Boiler Code for Boilers and Power Piping.
- Serves as the Site Contact for the Engineering Technical Services group to coordinate Site Matter Experts and Project Engineers as they interface with the station for projects, outages and site support activities.
- Responsible for identifying and coordinating training for station maintenance personnel.
- Responsible for identifying and executing projects designed to improve equipment reliability, station heat rate and reduce maintenance spend including EcoNRG projects.
- Responsible for maintaining the Site Configuration Documentation including databases, drawings and technical documents. Implements the site process for modifications.
- Supports Bill of Material, Procedure, Job Aids and Specification develop in support of station activities.
- Implement quality assurance procedures for critical spares and parts.
- Implements quality commissioning procedures for rebuilt or new equipment.
- Participates in best-practice sharing workshops to drive continuous improvements fleet wide.
- Plans, coordinates and implements a number of smaller (generally less than $200,000) construction projects directly or by directing/working with project teams, other Company organizations and outside suppliers.
- Independently or as a team member investigates fundamental problems in plant processes to initiate development of recommended solutions to provide the optimal safest, best environmental and economic solutions.
- Serves as Champion for the Root Cause Failure Analysis and Incident Reporting processes and develops corrective action plans to address findings and suggest strategies to prevent similar failures in the future.
- Provides/directs the development of reliable and cost effective conceptual engineering recommendations in response to plant maintenance, operational, safety and environmental needs, as assigned.
- Implements the Company process to obtain authorization of funding for assigned projects, reporting and maintaining expenditures within budget. This responsibility includes becoming one of the Power SAM site experts and project evaluation coordinators.
- Assures complete development of equipment specifications, bills of material, construction specifications, installation drawings, recommended spare parts, lists and as-built drawings.
- Monitors critical outage, maintenance and construction activities for compliance to applicable codes and standards.
- Performs outside vendor audits, QA shop surveillance, and interfaces with authorized inspectors.
- Executes all aspects of the start-up and test function on new plant systems and revisions to existing systems.
- Conducts and/or coordinates engineering performance tests on plant equipment and makes recommendations, when necessary, to improve efficiency.
- Provides technical, managerial and administrative functions on contracts with various contracted outside firms. Reviews all documents produced by outside consultants to assure conformance with Company policies and objectives, accepted standards, and appropriate engineering policies and procedures.
- Provides input to the five-year financial plans for both Operations & Maintenance and Capital in support of Hunterstown Combined Cycle and the Heritage Region CTs generating units.
- Supports the development and approval of projects and outages through the NRG Corporate Analysis and Commitment tools.
- Ensures optimum utilization of employees, equipment and material through the coordination of work between the organizational groups.
- Assumes other duties as assigned by Plant Manager of Hunterstown Combined Cycle and the Heritage Region CTs.
Required Qualifications
- Four (4) year Degree in Chemical or Mechanical Engineering with 5-10 years experience working with power/process plant equipment.
- Must have Combustion Turbine/Combined Cycle experience.
- Must have a valid driver's license
- Experience working with MS Word, Excel, Outlook and Access
Preferred Qualifications
- Experience working with SAP and AutoCAD
- OSIsoft PI Historian experience with PI ProcessBook
Other Essential Job Requirements
- Ability to provide direction to various operational and technical crafts
- Strong planning capabilities and the skills to analyze and interpret data to make sound recommendations to the Engineering Group Leader and to Senior Management.
- Strong customer focus (internally & externally)
- Strong problem solving and organizational skills
- Demonstrates initiative and adaptability
- Willingness to work off-hours as business needs dictate
- Internet experience
- Strong organizational skills
- Detail oriented
- Effective verbal and written communication skills
- Effective time and resource management skills
- Ability to direct, motivate, and train and employees
- Must be able to periodically travel to local plant locations and other NRG Sites for regional meetings, forums and training opportunities
Behavioral Attributes
- Demonstrates NRG Energy STRIVE Values, quick learner, shows initiative, strong planning, organizational and communication skills, ability to guide and develop a team, strong analytical skills.
Additional Notes on Compensation
Level, Title and/or Salary may be adjusted based on the applicant’s experience or skills.
Questions
There are no answered questions, sign up or login to ask a question
- Administrative
- AutoCAD
- Data Collection
- Databases
- Microsoft Access
- Microsoft Excel
- Microsoft Word
- Outlook
- Quality Assurance
- SAP
- Technical Services
- Testing
- Chemical Engineering
- Mechanical Engineering
- Resource Management
- OSiSoft PI
- Commercial Business Management
- Process Engineering
- Condition Based Maintenance
- PI ProcessBook
- SmartSignal
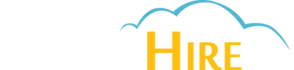
Want to see jobs that are matched to you?
DreamHire recommends you jobs that fit your
skills, experiences, career goals, and more.