Process Engineer
Caraustar
(Cincinnati, Ohio)Caraustar Industries, Inc. is one of North America’s largest integrated manufacturers of 100% recycled paperboard and converted paperboard products. The company is a socially responsible corporation, is committed to environmentally sound practices and is dedicated to providing customers with outstanding value through innovative products and services.
Provide technical support and training to a production department. Drive continuous improvement in the performance of all aspects of the operation – safety, quality assurance and customer service, productivity, operating efficiencies and cost containment.
- Support the Mill Safety Program completely. They must be fully involved in the safety culture and help drive the team towards an incident free workplace.
- Needs to be highly motivated and energetic providing leadership, technical support and training to guide changes to plant process and procedures in order to reduce process variability, improve product performance in customer plants, reduce manufacturing costs and improve operating efficiency.
- Support the mill's journey of continuous improvement. They must be able to learn, understand, and teach the Lean tools being utilized.
- Maintain specified equipment records. Purchase specified operating supplies.
- Facilitate the continuous improvement process by which projects and activities are identified, defined, developed and prioritized. Responsibilities include facilitating meetings, evaluating recommendations, planning and facilitating the implementation of changes, tracking activities and reporting progress.
- Participate in downtime maintenance and readiness planning and project management activities.
- Performs all required duties and tasks in accordance with Company accounting policies and financial control procedures.
- Provide support on all mechanical/electrical projects and activities.
- Train production employees in analytical problem solving and decision making techniques if applicable.
- Identify opportunities to improve existing procedures and related tools to meet the requirements of an evolving workflow process.
- Minimum Technical Background Requirement: Bachelor’s degree in chemical engineering, mechanical engineering or related technical field with 3-5 years’ experience in manufacturing, industrial or process engineering, product or technology development. Pulp and Paper degree and/or background is a plus.
- Process improvement knowledge in a manufacturing environment such as Lean Manufacturing, Six Sigma, etc., to drive operational excellence system is a plus.
- Statistical Process Control knowledge is desired.
- Proficiency in Parcview is a plus
- Ability to efficiently multi-task and meet/supersede stated objectives.
- Proficiency in Microsoft Office a must.
- Proficiency in data analysis a must.
- Must be able to communicate efficiently and effectively both written and verbal.
- Excellent team leadership abilities and interpersonal skills.
- Must be able to practice time management skills.
- Ability to adhere to healthy safety practices.
Questions
There are no answered questions, sign up or login to ask a question
- Adhereing to Safety Standards
- Cost Containment
- Customer Service
- Data Analysis
- Electrical
- Facilitating Meetings
- Manufacturing
- Operating
- Proficiency in Microsoft Office
- Project Management
- Quality Assurance
- Technical Support
- Chemical Engineering
- Mechanical Engineering
- Six Sigma
- Statistical Process Control (SPC)
- Process Engineering
- Lean Manufacturing
- Process Control
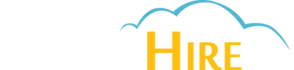
Want to see jobs that are matched to you?
DreamHire recommends you jobs that fit your
skills, experiences, career goals, and more.