Quality Technician
Hitachi
(Monroe, Georgia)Hitachi America, Ltd., a subsidiary of Hitachi, Ltd. established in 1959, is headquartered in Tarrytown, New York. Hitachi America, Ltd., and its subsidiary companies offer a broad range of electronics, power and industrial equipment and services, automotive products and consumer electronics with operations throughout the Americas.
Our recent expansion has afforded us an opportunity to seek a Quality Technician for our Quality Department at our Monroe, GA facility. You offer us your determination and work-ethic; we offer you very competitive pay and top-notch health benefits.
Performs product inspection assignments requiring use of instruments and techniques to measure quality levels of manufactured or purchased parts, in accordance with established procedures and/or standards
Support the review and establishment of programming of the Coordinate Measuring Machine (CMM) to complete daily inspections and work request.
Utilize inspection standards and best practices to create measurement routines with CMM, Optical Comparators and other various other lab equipment.
Support the Inspection Department as a trainer to team members.
-
Reviews all design drawings and changes, operation sheets, process procedures, test procedures, procurement documents, quality manuals, and inspection analyses to ensure the company’s and customers quality requirements are met on assigned products and programs.
-
Training of quality inspections teams and manufacturing associates on new and existing testing equipment and procedures.
-
Measure the capacity of testing equipment to meet testing requirements.
-
Develop, implement, maintain, and audit inspection standards for the review of raw materials and products at different stages in the receiving/manufacturing shipping process.
-
Manage and maintain the calibration of gages and the upkeep of the gage calibration system.
-
Lead projects to improve quality of processes, products and components as a result of internal/external findings or customer complaints. Perform joint analysis of complex problems with suppliers, design, manufacturing and other departments, to determine root cause and support development of countermeasures.
-
Leads or participates in Kaizen activities to analyze and develop countermeasures to customer complaints associated with processes, equipment, and completed parts.
-
Initiates and completes studies per work request such as Full Layouts and CPK, of all parts supplied to (HIAMS)AM-GA customers.
-
Document data, maintain database and develop computerized status reports related to inspection activities, nonconforming items, and other process, material or product quality related issues as required.
-
Establish, support, and monitor activities of the product sorting function and return of defective parts, including problem analysis, training and assignment.
- Minimum of three (3) years lab experience. Proficiency in programing CMM, reading GD&T drawings and completing product analysis, knowledge of calipers, micrometers, Vision Systems, and other measuring equipment. (preferably experience in automotive manufacturing environment)
- Customer-service, detail oriented, and can interact with customers and supply base professionally as needed.
- Ability to work with minimal supervision.
- Proven problem-solving skills.
- Excellent communications and interpersonal skills, including demonstrated leadership ability and ability to work as part of a team.
- Must be proficient in MSWord, Excel, and PowerPoint.
Questions
There are no answered questions, sign up or login to ask a question
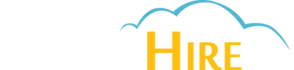
Want to see jobs that are matched to you?
DreamHire recommends you jobs that fit your
skills, experiences, career goals, and more.