Maintenance Engineer
Dr Pepper Snapple Group
(Los Angeles, California)Dr Pepper Snapple Group, Inc. (NYSE: DPS) is the leading producer of flavored beverages in North America and the Caribbean. Our success is fueled by more than 50 brands that are synonymous with refreshment, fun and flavor. We have 6 of the top 10 non-cola soft drinks, and 11 of our 14 leading brands are No. 1 in their flavor categories.
The Facilities Maintenance Engineering Manager enhances service quality and equipment reliability by improving workflows and optimizing maintenance processes using Lean Six Sigma practices and Reliability Centered Maintenance (RCM) methodology. This position, a key link between the field maintenance organization and the engineering and manufacturing centers, provides input to improve equipment design, reliability, and maintainability.
The Facilities Maintenance Engineering Manager has a critical role in connecting field operations with the maintenance organization, helping minimize downtime and failure rates and maximize equipment productivity. This position reports directly to the Plant Manager. To execute, position obtains and develop resources, manage your team and 3rd party contractors. Identify, assess, and minimize technical risks through successful project tasks delivery. Objective is to drive projects to successful completion, resulting in highly satisfied customers and product solutions which support the business growth objectives.
- Oversee the installation of all facility equipment.
- Keeps current with latest equipment, technologies, and maintenance methods.
- Identifies and captures opportunities for improvement in equipment maintainability and reliability.
- Supports Maintenance Manager and TPM Manager in planning for equipment and maintenance resources and correcting existing discrepancies.
- Oversee work, set or edit standards, policies and procedures for vendors and contractors
- Manage financial aspects of the operation area including annual budget development, capital planning and administration.
- Oversee all facility housekeeping contracted with janitorial vendor (office and critical environment cleaning)
- Participates in technical audits and compliance assessments, and follows up on closure of remedial action plans
- Assists with development and coaching of junior maintenance staff.
- Ensures application of asset management and maintenance systems data and accurate, timely data entry and reporting.
- Establish clear ownership for project tasks within the team and a clear schedule for when each task will be performed. Ensure that team members have the tools needed, and provide timely feedback.
- Work collaboratively with peer Engineering managers within the company to drive network initiatives, balance resource demands, and coordinate global team interaction.
- Uses Lean Six Sigma and RCM concepts to optimize work processes, adapt maintenance tools and procedures to improve equipment utilization and reliability, and minimize service quality incidents.
- Promotes importance of data and service quality within TPM/ maintenance community.
- Mandatory On-call availability to respond to all facility emergencies
- Performs other duties as assigned within the scope of the position.
- Conduct regular status meetings with all stakeholders, keeping the stakeholder’s needs and requirements continuously in view.
Knowledge and Skills:
- Knowledge of bottling/can manufacturing.
- Lean/Six Sigma certifications/training.
- Demonstrated supervisory, organizational and interpersonal ability.
- Ability to problem solve and multitask.
- Basic understanding of labor and federal regulations.
- SAP manufacturing applications and strong computer skills.
- Strong communication and leadership skills.
- Demonstrated understanding and proven implementation of TPM/5S.
- Aptitude for hands-on work coupled with analytical skills.
- Ability to solve problems via advanced technical knowledge, complex analysis and theory testing.
- A record of success in implementing lean manufacturing concepts for continuous improvement (TPM/5S).
- Experience with spending most of the time on the manufacturing floor. This is not a manage via the office position
Qualifications:
- Bachelor's degree in engineering or applied science.
- 3 year of engineering team management experience.
- 3 years of leadership experience in managing others.
- 3 years of experience working with electrical, electronic and mechanical maintenance in the bottling industry.
Questions
There are no answered questions, sign up or login to ask a question
- Administration
- Computer
- Data Entry
- Electrical
- Electronics
- Maintenance
- Mechanical
- SAP
- Team Management
- Technical Knowledge
- Asset Management
- Budget Development
- Capital Planning
- Knowledge of Revenue Cycle Management
- Reliability Centered Maintenance
- engineering
- Lean Six Sigma
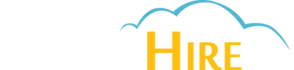
Want to see jobs that are matched to you?
DreamHire recommends you jobs that fit your
skills, experiences, career goals, and more.