Capital Project Engineering Manager Job
Armstrong World Industries
(Lancaster, Pennsylvania)Armstrong World Industries, Inc. (AWI) is a global producer of flooring products and ceiling systems for use in the construction and renovation of residential, commercial and institutional buildings. The Company designs, manufactures and sells flooring products (resilient and wood) and ceiling systems (mineral fiber, fiberglass and metal) globally. The Company segments includes: Building Products, Resilient Flooring and Wood Flooring.
Under the direction of the Director of Engineering, the Capital Project Engineering Manager has global responsibility for, 1) Executing capital projects, 2) Defining the best practice execution process, standard work, and engineering and reliability standards, 3) Capital management including strategic capital planning, annual capital planning and execution of the operating plan capital.
Project Execution -- Safety, Cost, Schedule, and Performance:
- Execute capital projects to safety, cost, schedule, and performance commitments
- Execute capital projects using WAVE business process and standard work
- Mentor and lead project teams to execute projects using defined business processes and standard work
- Use precision maintenance principles and ITPs (Inspect and Testing Plans) to design, fabricate, and install highly reliable and capable assets.
- Use CMMS to help manage storeroom inventory and major spare parts
Best Practice Capital Project Execution – Standard Work:
- Advance capital execution process and standard work – continuous improvement based on Lean and Reliability principles. Visual management is a critical element.
- Critical methods include, cost management, schedule management, risk and change management.
- Align with Armstrong ABP and Worthington to leverage processes, standard work, procurement, technical support, and training
- Define engineering standards for processes, assets, controls, and utility services –including preferred equipment lists, installation specifications, drawing standards, etc.
- Develop simple plant self assessments to check current state to the standards and ensure plant maintenance and project activities are aligned to the standards
Skill Development and Capacity – Engineering & Reliability Competencies:
- Manage a technical organization consisting of engineers, designers, craftsman, and reliability specialist.
- Define the engineering, design, reliability, project controls, and project execution competencies and skills required in the plant, engineering, and technical support groups
- Define, assess, and map the current state of skills in the organization
- Develop plans and training require to upgrade skill and stay current with technology changes
- Mentor the plant engineers & project engineers on best practices and transfer learning to develop global talent.
- Develop a network of external contractors and engineers to support WAVE needs for project and plant technical support to drive cost improvements and process effectiveness and reliability
Reliability Leadership:
- Participate in setting a reliability direction for WAVE globally – based on precisions maintenance and PdM principles.
- Define ITP standards by asset type and drive engineering and maintenance efforts to ensure assets are designed, fabricated, installed and maintained to these standards.
- Lead reliability improvement efforts on assets and process.
- Facilitate/lead teams through good problem solving and Lean methodologies for step changes in reliability and capability
- Participate in strategic planning sessions to set the direction for future technology platforms & reliability standards
Capital Management & Planning – 3 to 5 Year Investment Plan:
- Develop a 3 to 5 year global strategic capital investment plan
- Facilitate an annual capital planning process resulting in an annual capital budget by plant – align the capital plan to the WAVE operating plan and P&L
- Manage the annual global capital spend and capital appropriation approvals – track key measures of capital execution.
- Identify and drive continuous improvement for improve capital management and execution
- Coordinate projects across plant and generations of technologies as required to improve productivity, reliability, and capability and reduce the highest risk in the plants
Measures of Effectiveness
- Safety Performance: no injuries on projects, compliance to codes, and evidence of reducing risks
- Projects – meet cost, schedule, and performance commitments
- Productivity – increased PE (process effectiveness) and MLF/Man hour metrics
- Headcount – reduce FTEs (full time equivalents) in the plants through automation and productivity
- Project Assessment Scores – health of projects relative to standards and best practices
- Capital management metrics
- 10 years manufacturing experience in engineering and project execution, required
- 3 – 5 years managing and/or mentoring of engineers, craftsman, and contractors, required
- BS degree in Engineering or equivalent, required
- MBA, preferred
- Project management experience, required
- Reliability and predictive maintenance experience, required
- Global project execution and technical support, preferred
- Applied knowledge of lean manufacturing practices, preferred
Benefits | Benefits not included |
---|
Questions
There are no answered questions, sign up or login to ask a question
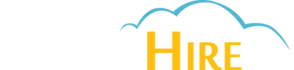
Want to see jobs that are matched to you?
DreamHire recommends you jobs that fit your
skills, experiences, career goals, and more.