Maintenance Manager
Amy's
(Pocatello, Idaho)Founded 28 years ago in Sonoma County, California, Amy's Kitchen is a world leader in the production of natural and organic convenience foods. Named after Andy and Rachel Berliner's daughter, Amy, the company now has over 2,400 employees. Yet, it remains a privately held, family-owned business and is one of the few remaining U.S. companies to craft its own recipes, source its own ingredients, and make its products in-house.
The Maintenance Manager is responsible for the overall administration of the Maintenance Department. It is the Manager’s responsibility to ensure that the Department is following Company rules and guidelines. In addition the Maintenance Manager must direct the Maintenance personnel in order to maintain and repair a variety of manufacturing/processing/packaging equipment. He / She establishes and maintains schedules and controls to provide continuous, preventive, routine and emergency repairs to all manufacturing equipment and building structures. This requires that activities be self-initiated and self-directed, as well as responsive to needs as defined. He / She advises and provides technical data required to implement maintenance programs for existing and new equipment; must also have good electrical, pneumatic and mechanical troubleshooting skills. He / She must be detail oriented, with excellent personal skills.
- Supervise Maintenance personnel in performing repairs and maintenance activities for material handling and food processing equipment.
- Supervise Maintenance personnel in performing repairs and maintenance activities to all building structures and grounds.
- Develop and maintain preventative maintenance program including scheduling of service or repair work for each piece of equipment.
- Develop and maintain spare parts inventory including supplies. Responsible for establishing stock status, minimum and maximum and maximum inventory levels (reorder point).
- Prioritize, schedule and assign work activities using work order system.
- Coordinate the maintenance, repair and troubleshooting of manufacturing equipment.
- Coordinate the troubleshooting, and repair/service of all refrigeration equipment.
- Provide necessary training and coaching to all the Maintenance personnel.
- Responsible for maintaining staff levels as defined. Responsible for (with support from the HR Department) the interviewing, hiring, and firing of Department employees.
- Provide activity and project status report to the Plant Manager due at the end of each month. This will be done through a project summary memo.
- Develops and maintains Maintenance department budget.
- Conduct studies of existing equipment problems; analyze alternative solutions, and provide conclusion and recommendations to the Plant Manager.
- For minor projects using outside services, (contractors); the Manager must develop project specifications; conduct pre-bid information meetings with contractors, gather contractor bids; analyze and award bids; schedule and supervise equipment installations.
- Provide or arrange for supervision coverage on weekends.
- On all projects over $5,000.00, obtain three competitive bids. Exceptions must be explained and documented.
- Complete and obtain all contractor paper work and place on file in Maintenance office. This includes certificates of insurance (general liability and workers comp.), purchase orders and contractor’s handout (reviewed and signed).
- Coordinate all project activities between Department/contractor and the plant departments involved. Ensure that all Company rules are enforced, as well as, local, state and federal laws, (i.e. OSHA).
- Conduct daily (or as needed) information and planning meetings on major projects/events requiring the coordination of activities with other departments, Amy’s personnel, or contractors.
- Provide technical support to all plant departments on an as-needed basis.
- Responsible for department safety record. Monitor Maintenance personnel's adherence to safety rules including following lockout/tag out procedures during repair, adjustments and servicing of equipment. Follow disciplinary procedures to correct unsafe acts.
- Comply with the rules and regulations set forth in Amy's Kitchen Inc. employee handbook, safety manual, the GMP booklet, and HACCP program.
- Perform other tasks as assigned.
Education
BS Degree in an Engineering from four-year college or university; or equivalent combination of education and experience.
Experience
A minimum of 10 years of experience as a Maintenance Supervisor / Manager in a similar manufacturing environment is required.
Skills
- Proficiency with PLC’s, Servo system troubleshooting/programming recommended.
- Proficiency in interpreting electrical, pneumatic, hydraulic, and mechanical drawings is recommended.
- Must be PC literate, with a working knowledge of Microsoft Word, Excel and Outlook, on a Windows 2000 or later version operating system.
Language Skills
- Able to read and comprehend instructions, correspondence, and memos.
- Ability to write correspondence.
- Able to effectively present information in one-on-one and group situations to other employees of the organization.
Certificates, Licenses, Registrations
Refrigeration license for Freon / Ammonia systems a plus.
Reports to | Plant Engineering Manager |
---|
Questions
There are no answered questions, sign up or login to ask a question
- Electrical
- Equipment
- Inventory
- Maintenance
- Manufacturing
- Mechanical
- Microsoft Excel
- Microsoft Outlook
- Microsoft Word
- Refrigeration
- Repairs
- Troubleshooting
- Hydraulics
- Good Manufacturing Practice (GMP)
- engineering
- Pneumatics
- HACCP
- Programmable Logic Controller (PLC)
- Windows 2000
- Personal Computer (PC)
- Work Order
- Servo control systems
- Occupational Safety and Health Administration
- Mechanical Drawing
- Lockout Tagout
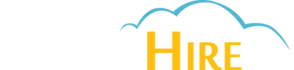
Want to see jobs that are matched to you?
DreamHire recommends you jobs that fit your
skills, experiences, career goals, and more.