Corporate Quality Manager
Spectrum Brands
(Lake Forest, California)Spectrum Brands Holdings, a member of the Russell 2000 Index, is a global and diversified consumer products company and a leading supplier of consumer batteries, residential locksets, residential builders’ hardware, plumbing and accessories, shaving and grooming products, personal care products, small household appliances, specialty pet supplies, lawn and garden and home pest control products, personal insect repellents, and auto care products.
The Corporate Quality Manager will elevate quality as a competitive advantage and drive brand loyalty by ensuring high product quality from design through production. The Quality Manager will direct the corporate quality organization focused on product, process and design quality and will advance leading practices to provide predictable results and excellent customer experiences. The Quality Manager applies strategic directives to prioritize, develop, implement and own effectiveness of all QA functions that support worldwide product, process and management through quality systems. The QA Manager will lead, coach and reinforce the foundations of a corporate quality culture and ensure empowerment of direct reports and extended matrix organizations.
- Responsible for creating an empowered quality culture within core and extended matrix organizations.
- Inspire trust, clarify purpose, unleash talent and align process and systems to meet vision and mission objectives.
- Responsible for prioritizing, development and deployment of achievable initiatives to meet objectives while applying strategic vision to meet corporate goals
- Lead, coach and mentor the Global Quality Assurance Team. Responsible for the Organization and People Review (OPR) process for the US Quality team including the support of their Individual Development Plans.
- Interfaces with customers, marketing and sales to identify requirements, ensure alignment of balanced expectations, and plan proactively for corrective action and continuous improvement.
- Model the Spectrum Brands eight Core Capabilities to achieve service excellence, meet and exceed organizational objectives and support fiscal responsibility.
- Serve as the Coach and leader of the New Product Qualification Process (PQP). Some the key steps include: VOC analysis, Critical To Quality (CTQ) creation, Control Plan, FMEA, Capability Analysis, and reliability testing.
- Direct and coach the QA and Supplier teams to ensure successful product launches through pilots and production readiness programs. Effectively sustain factory and supplier product quality through production lifecycle phases.
- Direct the Request for Investigation (RFI) and Request of Corrective Action (RFCA) process to improve customer satisfaction. This should be translated into reduction of Cost of Quality, decline of defective returns, and improved of consumer reviews.
- Establish clear metrics and goals to meet vision and mission objectives. Provide visibility to top management on the performance of key indicators of Cost of Quality, status and own development of the Quality Management System, status and own critical continuous improvement activities.
- Prioritize, Institute and execute initiatives focused on supplier key business processes that influence customer satisfaction, waste elimination, growth, cost effectiveness, and product/system quality.
- Partner, Coach and lead the Supplier Quality Engineering team in Asia to ensure that corrective actions are properly validated and that manufactured products meet customer requirements.
- Proven experience in culture and system change management
- Proven leadership in Project Management in a multi-departmental matrix leadership organization.
- Ability to make decisions, communicate effectively and work effectively with external and internal customers.
- Proven experience communicating to upper management on an ongoing basis.
- Proven experience leading the use of 8D and/or DMAIC lean six sigma methodology for closing Corrective & Preventive Actions.
- Proven experience leading and facilitating cross functional Kaizen/Workshops on new product or process development.
- Experience with APQP process (PPAPs, Control Plans, FMEA, etc.)
- Preferred experience with Design for Six Sigma Tools (QFD, CTQ Flowdown & Measurement Systems, DOE, DFR, DFM, etc…)
- Demonstrated knowledge and ability to apply statistical tools and methods to problem solving in a quality or process improvement arena.
- Excellent interpersonal skills and ability to work with others positively.
Education and Experience Profile
- Bachelor's degree in Engineering or closely related. MBA preferred.
- 7 - 10 years of progressive experience in Quality Assurance with duties involving supplier/advanced quality assessment in a high volume manufacturing environment.
- Certified Black Belt or equivalent preferred
- ASQ Certified Quality Manager preferred
- Consumer Product Manufacturing experience preferred
- Experience working with plumbing products is a plus
Working Conditions
Working conditions are normal for an office environment.
Questions
There are no answered questions, sign up or login to ask a question
- Design
- Effectiveness
- Empowerment
- Interpersonal
- Leadership
- Making Decisions
- Management
- MBA
- Plumbing
- Problem Solving
- Project Management
- Quality Assurance
- Dmaic
- Design for Manufacturability
- High Volume Manufacturing
- Failure mode and effects analysis (FMEA)
- Statistical Tools
- Advanced Product Quality Planning (APQP)
- Design for Six Sigma
- Design For Reliability
- QFD
- Bachelor’s Degree
- Quality Culture
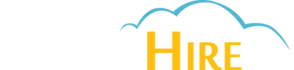
Want to see jobs that are matched to you?
DreamHire recommends you jobs that fit your
skills, experiences, career goals, and more.