Health, Safety, and Environmental Manager
Amy's
(Santa Rosa, California)Founded 28 years ago in Sonoma County, California, Amy's Kitchen is a world leader in the production of natural and organic convenience foods. Named after Andy and Rachel Berliner's daughter, Amy, the company now has over 2,400 employees. Yet, it remains a privately held, family-owned business and is one of the few remaining U.S. companies to craft its own recipes, source its own ingredients, and make its products in-house.
Establishes and promotes the maintenance of a safe work environment by managing the Environmental, Health, and Safety Program for the manufacturing facility they serve. Sets and maintains a safety culture that encourages safety awareness and self responsibility. Leads plant focus on all aspects of occupational safety. Formulates policies and procedures in line with safety regulations and to reflect the safety aspect of manufacturing. Educates, mentors, and trains peers and fellow employees in safety concepts, responsibilities and safe work practices. Provides technical guidance, training and inspection on risk analysis in plant environment for staff to ensure compliance with Environmental Protection Agency, Occupational Safety & Health Administration, Fire Code, Department of Environmental & Natural Resources, Insurance Companies, and Department of Emergency Management standards and regulations. Regularly audits the various elements of the entire Safety Program for robustness of, and adherence to, the program. Leads corrective and preventive action for any deficiencies. - See more at: http://www.amys.com/about-us/employment#job-RS9529761028
Safety
- Actively engages the workforce and management to promote and develop a safety culture.
- Develops, implements, maintains and improves company policies, processes and procedures relating to occupational safety.
- Interacts with all local, state, and federal regulatory agencies relating to occupational safety issues. Provides all required reports and information to the Plant Manager in a timely manner.
- Prepares regulatory required reports for outside enforcement agencies.
- Provides regular reports to management relating to company safety performance.
- Develops, reviews and revises written safety related plans. Leads corrective and preventive actions process to ensure successful completion of plant safety objectives.
- Leads effort to regularly audit and validate effectiveness of all machine-specific LOTO procedures.
- Develops and manages the facility safety incentive programs.
- Directs, supervises, develops and coordinates wellness-related programs for faculty and staff in plant
- environment.
- Partners with Human Resources in managing the company Return to Work program.
- Participates in, and actively promotes plant management Safety Walk program. Tracks pending corrective action plans from Safety Walks. Audits implemented corrective action plans to ensure continued compliance.
- In conjunction with Manufacturing Managers/Supervisors, performs post accident investigation and reporting to identify root cause and create an action plan. Coordinates meeting with employee, Shift Leader/Supervisor, Manager and Plant Manager to review accident/incident and discuss corrective action plan. Coordinates sessions with the Physical Therapist and Employee. Helps manage implementation of action plan. Recognizes when a corrective action plan could apply to other Amy’s manufacturing plants and communicates the corrective action plan to the other plant’s Safety Manager and Plant Manager.
- Audits accident reports and follows up with Manager when deficiencies need to be addressed.
- Audits adherence to safety accident/incident corrective action plans.
- Directs/supervises safety inspection/risk analysis services for all departments to identify/abate recognized safety hazards/loss exposures. Completes Job Hazard Analysis, Taproot or Root Cause Analysis, Near Miss, Post Incident.
- Manages all safety groups such as committees and teams (Safety Team).
- Trains/certifies power truck operators and aerial lift operators along with First Aid Team members in Red Cross specific training requirements.
- Responsible for planning, organizing, developing, and implementing various required occupational safety training.
- Manages and conducts new employee orientation in regards to company safety policies.
- Manages Safety Department budget.
- Performs site safety audits and inspections, completes comprehensive report of findings, including remediation/correction plan, enforce compliance.
- Designs and directs programs to reduce accidents, injuries and occupational illnesses. Implements pre- and post-loss controls to avoid or lessen loss and liability.
- Develops and implements Health, Safety and Environmental Programs, including training.
- Responds to, investigates, and resolves employee safety concerns.
- Develops and disseminates safety materials, publications, safety minutes, OSHA bulletins.
- Maintain and update HSE Manual.
Hazardous Materials
- Develops and maintains Hazardous Materials Business Plan for the facility.
- Ensures compliance with regulatory guidelines and requirements.
- Interacts with local, state and federal regulatory agencies relating to hazardous materials. Provides all required reports and information to the Plant Manager in a timely manner.
- Directs/supervises multi-dept hazardous, medical and universal waste disposition in accordance with local, state and federal regulations.
- Maintains training matrixes as required.
- Serves as subject matter expert as required.
Fire Prevention
- Interacts with all local, state, and federal regulatory agencies relating to Fire Prevention. Provides all required reports and information to the Plant Manager in a timely manner.
- Performs internal and external inspections and audits relating to Fire Prevention.
Workers Compensation Claims Management
- Assists in reporting Workers Compensation claims. Assists insurance claim adjusters as needed.
- Assists in claims experience reporting and analysis of loss data.
- Develops and administers Early Return to Work Program.
SUPERVISORY RESPONSIBILITIES
- Directly manages Safety Department personnel. Carries out supervisory responsibilities in accordance with the organization’s policies and applicable laws. Responsibilities include interviewing, hiring, and training employees planning, assigning, and directing work; appraising performance; rewarding and disciplining employees; addressing complaints and resolving problems.
- To perform this job successfully, an individual must be able to perform each essential duty satisfactorily. The requirements listed are representative of the knowledge, skill, and/or ability required. Reasonable accommodations may be made to enable individuals with disabilities to perform the essential functions.
EDUCATION and/or EXPERIENCE
- Bachelor's degree (BA or BS) in related field and 2-5 years of experience in Industrial Safety, or Training/Certification in safety management and 5-7 years of related experience.
LANGUAGE SKILLS
- Ability to read, analyze, and interpret general business periodicals, professional journals, technical procedures, or governmental regulations in English (and Spanish, where applicable).
- Ability to write reports, business correspondence, and procedure manuals in English (and Spanish, where applicable).
- Ability to effectively present information and respond to questions from groups of managers, clients, customers, and the general public in English (and Spanish, where applicable).
MATHEMATICAL SKILLS
- Ability to work with mathematical concepts such as probability and statistical inference, and fundamentals of plane and solid geometry and trigonometry.
- Ability to apply concepts such as fractions, percentages, ratios, and proportions to practical situations.
REASONING ABILITY
- Ability to define problems, collect data, establish facts, and draw valid conclusions.
- Ability to interpret an extensive variety of technical instructions in mathematical or diagram form and deal with several abstract and concrete variables.
CERTIFICATES, LICENSES, REGISTRATIONS
- None
PHYSICAL DEMANDS
- The physical demands described here are representative of those that must be met by an employee to successfully perform the essential functions of this job. Reasonable accommodations may be made to enable individuals with disabilities to perform the essential functions.
WORK ENVIRONMENT
- While performing the duties of this job, the employee is routinely exposed to wet and/or humid conditions, outside weather conditions, extreme cold, and extreme heat. The noise level in the work environment is moderate to loud.
Reports to | Plant Manager |
---|
Questions
There are no answered questions, sign up or login to ask a question
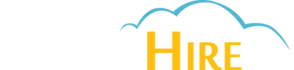
Want to see jobs that are matched to you?
DreamHire recommends you jobs that fit your
skills, experiences, career goals, and more.